Overview
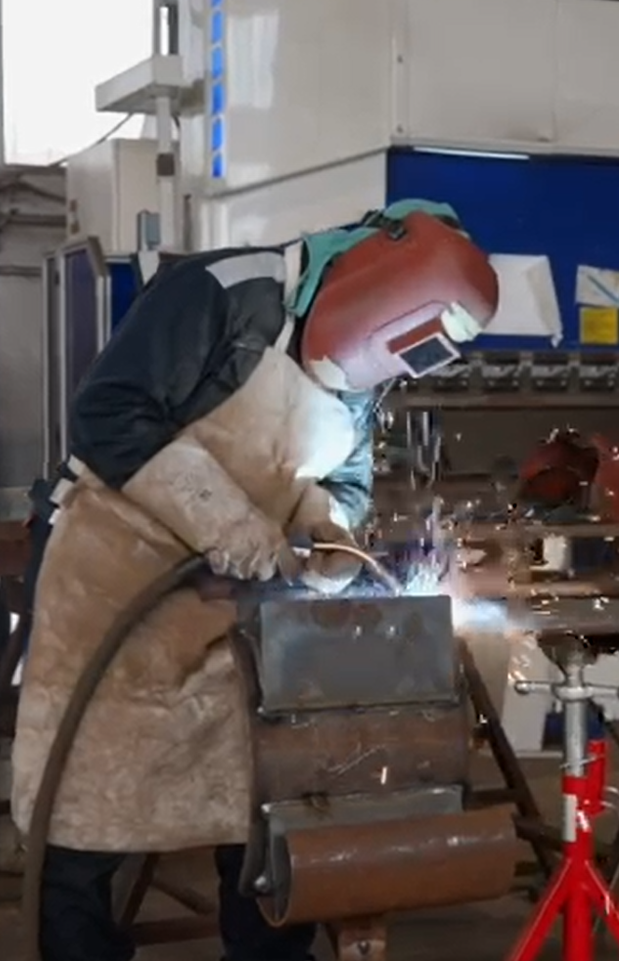
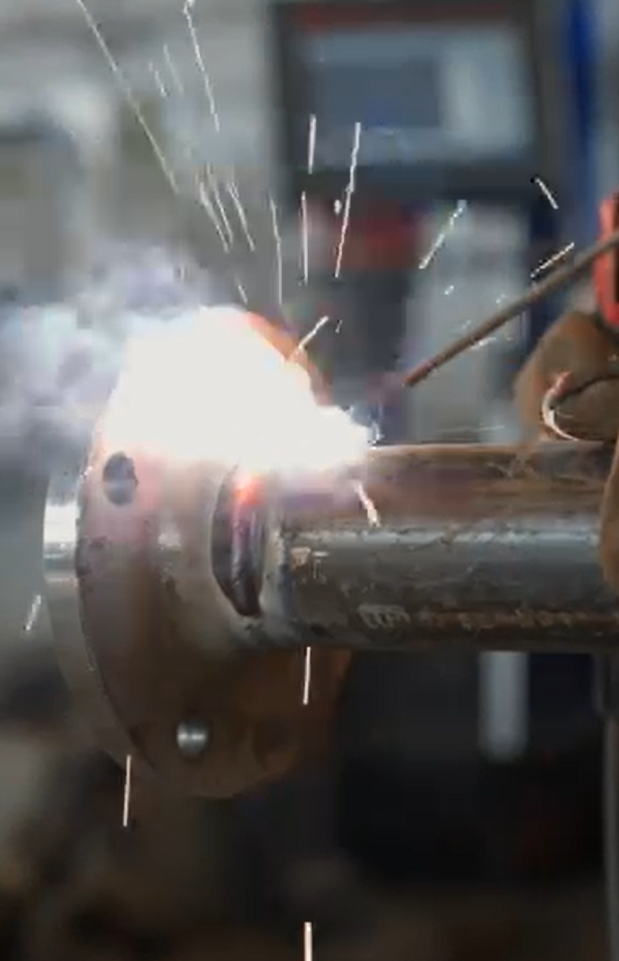
Construction & Assembly Tecta S.r.l. specializes in the prefabrication and assembly of piping systems, alongside the supply and installation of steel structures. The construction of steel carpentry involves multiple complex phases, which Tecta supports through substantial investments in state-of-the-art equipment and advanced operational capabilities.
These resources, combined with a team of highly qualified professionals, allow the company to organize both permanent and mobile construction sites that operate autonomously to execute projects efficiently.
All activities are performed in strict compliance with safety and environmental regulations, adhering to ISO 45001:2018 and ISO 14001:2015 certified management systems. This commitment ensures the highest standards of health, safety and sustainability
Main Projects
2020: Construction of an AISI 316 Stainless Steel Tank
The project involved the engineering, fabrication, and installation of an AISI 316 stainless steel tank, specifically designed for the safe storage and handling of corrosive or high-purity fluids in an industrial setting. Given the material’s exceptional resistance to chemical agents, high temperatures, and oxidation, the tank was tailored to meet stringent industry requirements for durability and performance.
The scope of work included precision cutting, automated and manual TIG/MIG welding to ensure high-integrity seams, and surface finishing treatments such as passivation and pickling to enhance corrosion resistance. Rigorous quality control procedures, including non-destructive testing (NDT), hydrostatic pressure tests, and dimensional inspections, were carried out to guarantee compliance with international safety and operational standards. Additionally, structural reinforcements and advanced sealing solutions were integrated to prevent leaks and ensure long-term reliability. The project was executed under strict safety protocols, ensuring optimal performance, extended service life, and seamless integration with existing plant infrastructure.
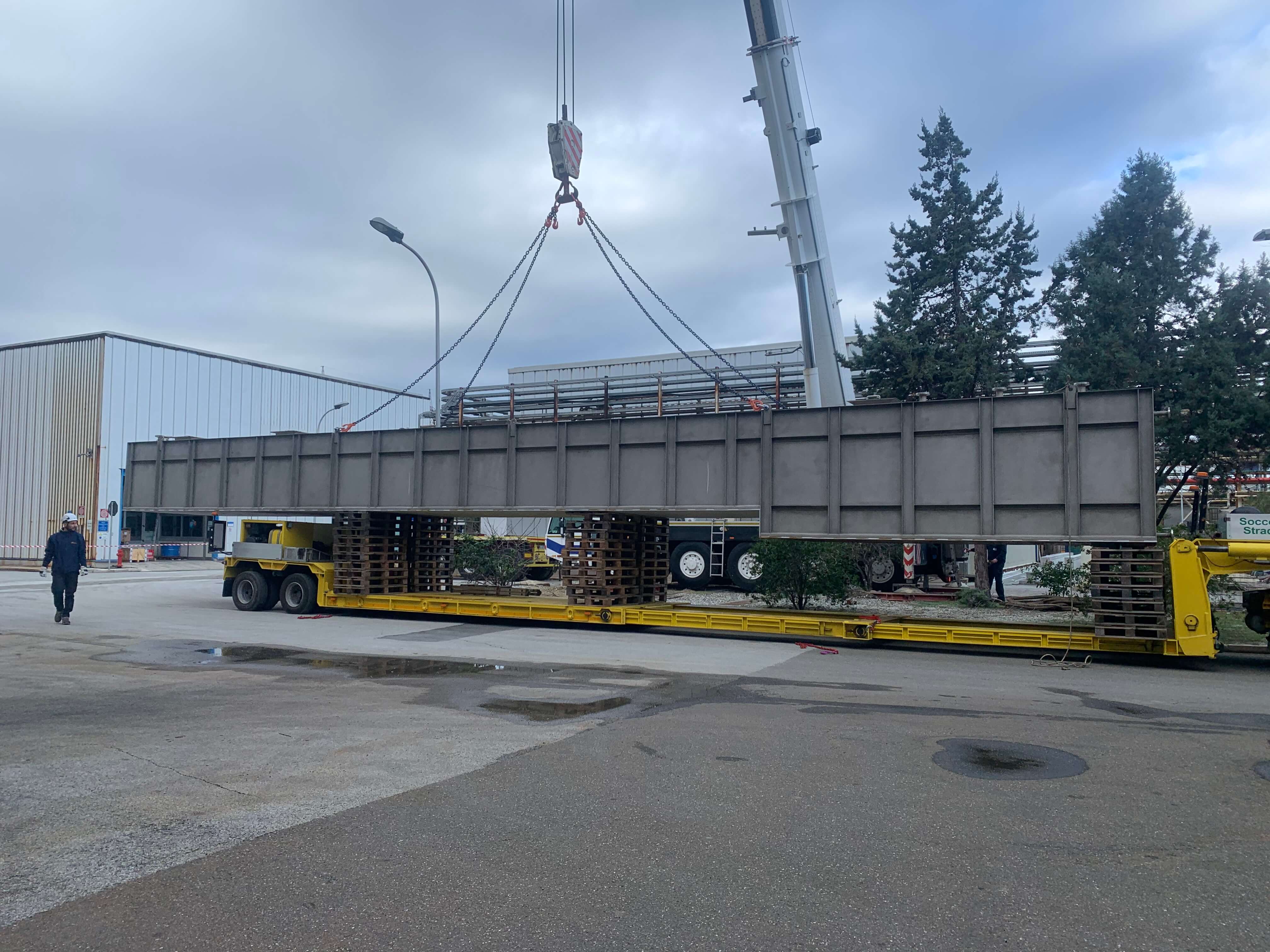
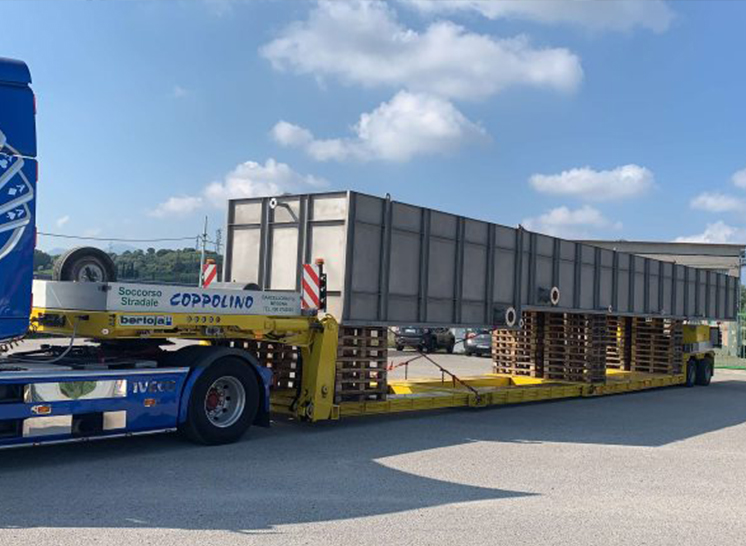
2019: Mechanical Piping and Steel Structure Activities for the Completion of the Tolone Marghera Project
The project focused on the mechanical piping and steel structure works required for the completion of the Tolone Marghera project, including the fabrication, installation, and alignment of complex piping networks designed to handle high-pressure and corrosive substances, ensuring reliable and efficient plant operations. The scope of work involved precision welding, pipe fitting, and the installation of support systems tailored to withstand mechanical stress and thermal expansion. The steel structure tasks included the erection of load-bearing frameworks, platforms, and access ladders, all engineered to meet rigorous safety and structural standards. Special attention was given to integrating these systems seamlessly into the existing plant layout, minimizing operational disruptions.Throughout the project, stringent quality assurance measures were in place, including non-destructive testing (NDT) of welds, hydrostatic testing of piping systems, and regular compliance checks to meet industry regulations. The project was carried out with a strong emphasis on safety, operational efficiency, and meeting deadlines, ensuring smooth plant operations post-completion.
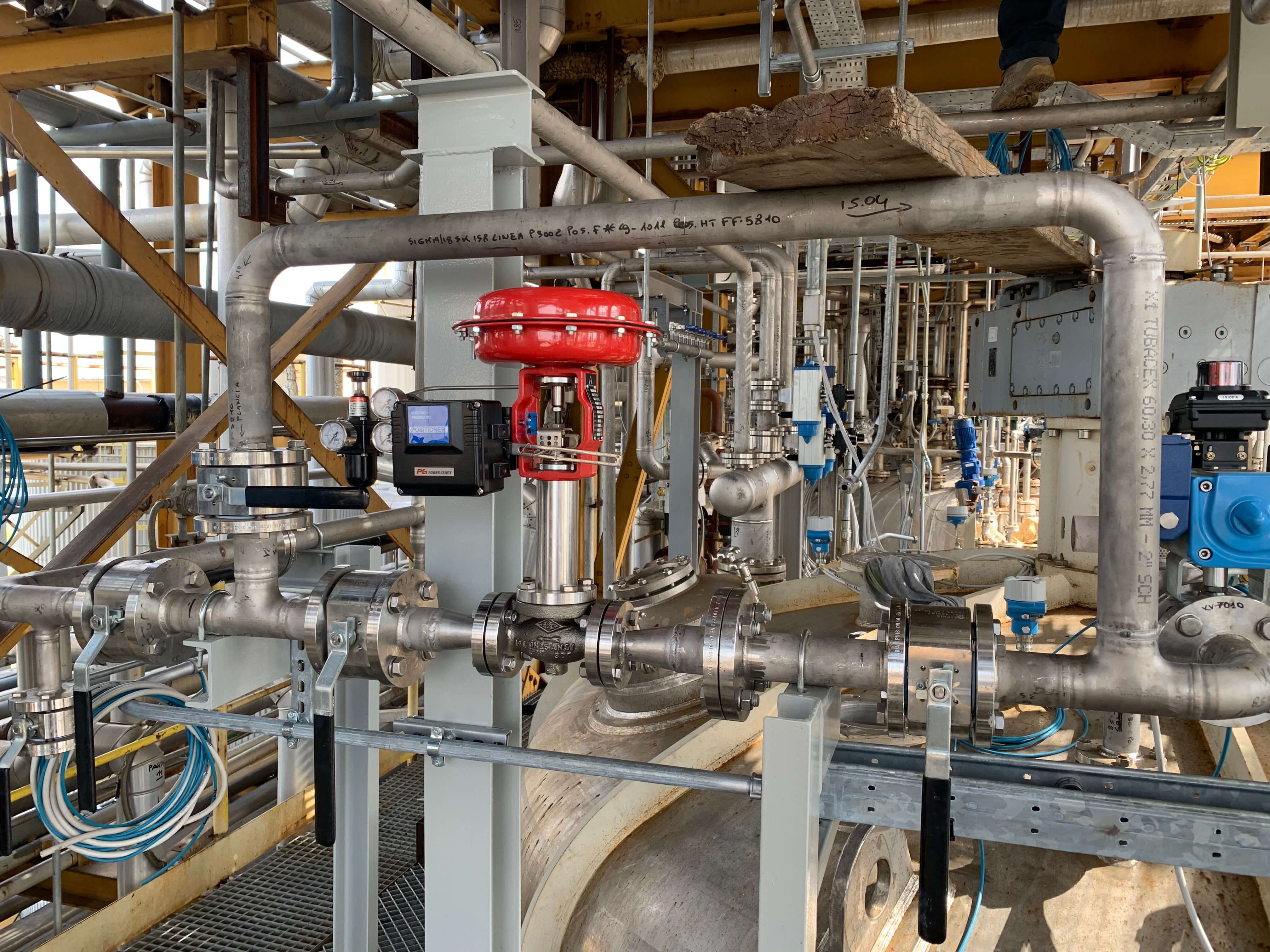
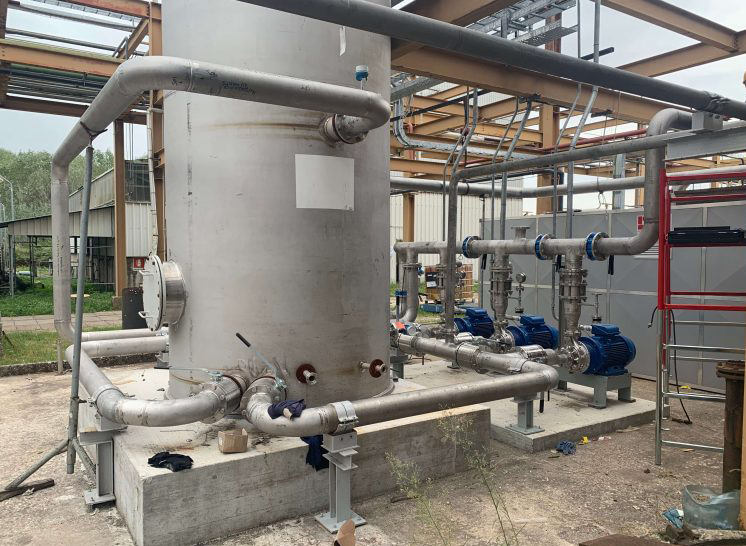
2018: Assembly of the Concentration Plant (API Schmidt-Bretten) with Related Piping ConnectionsThis project focused on the installation and assembly of the Concentration Plant (API Schmidt-Bretten), paired with the essential piping systems required for fluid transportation.
The assembly process involved coordinating various plant components and ensuring proper integration into the operational framework.The piping system, designed to carry high-pressure fluids, was carefully routed to minimize any operational disruption.
Material selection for the pipes, valves, and fittings was done with durability in mind, ensuring the system would withstand the demanding conditions of the plant. Special attention was paid to the installation of each pipe segment, ensuring a precise fit and reliable connections.
Quality control measures included extensive testing of the piping system for pressure resistance and leak detection. Non-destructive testing (NDT) was conducted on all welded joints, ensuring they met rigorous standards for both strength and safety. The installation was completed with a focus on meeting timelines and optimizing the plant’s functionality for future operations.
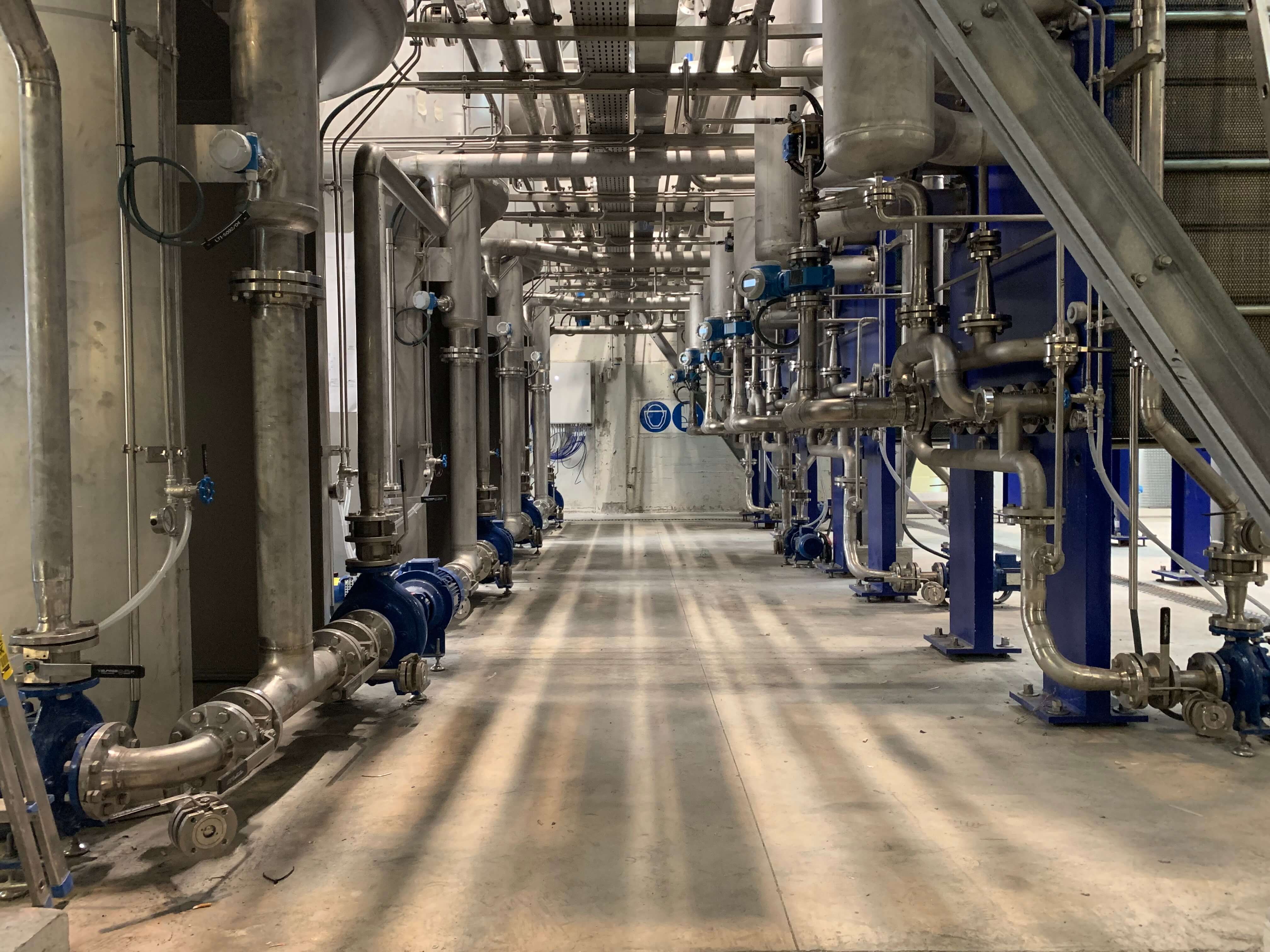
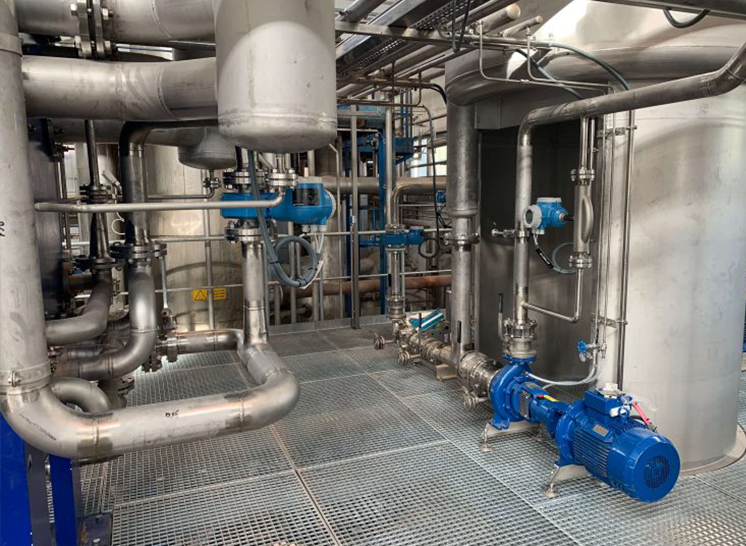
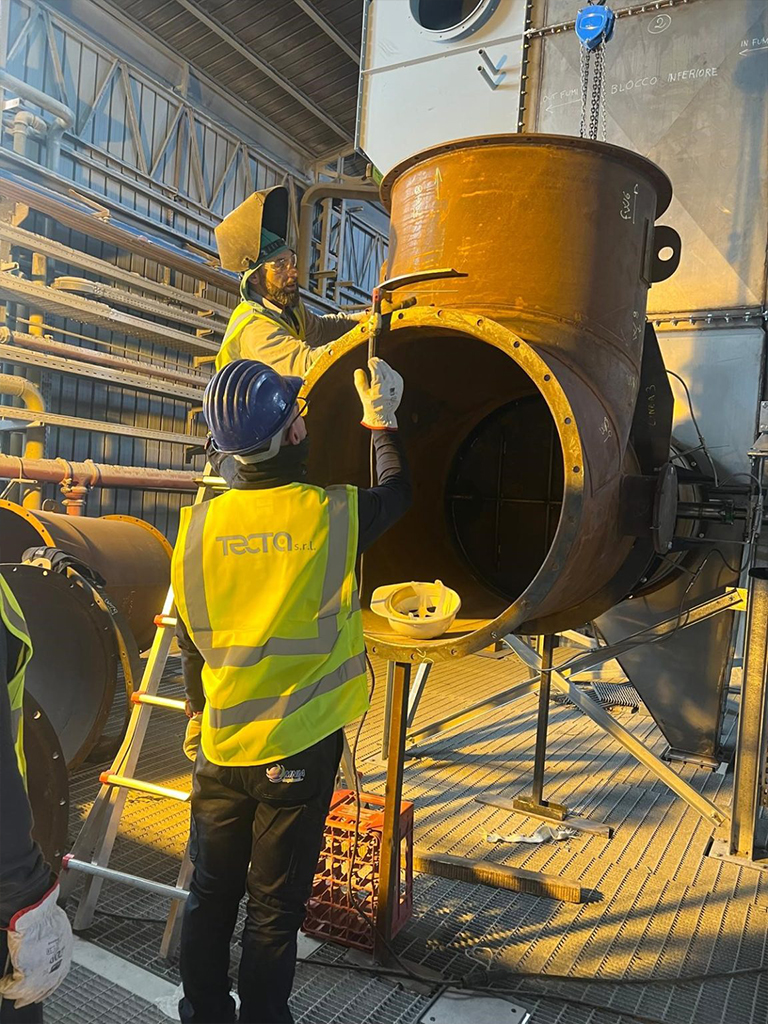
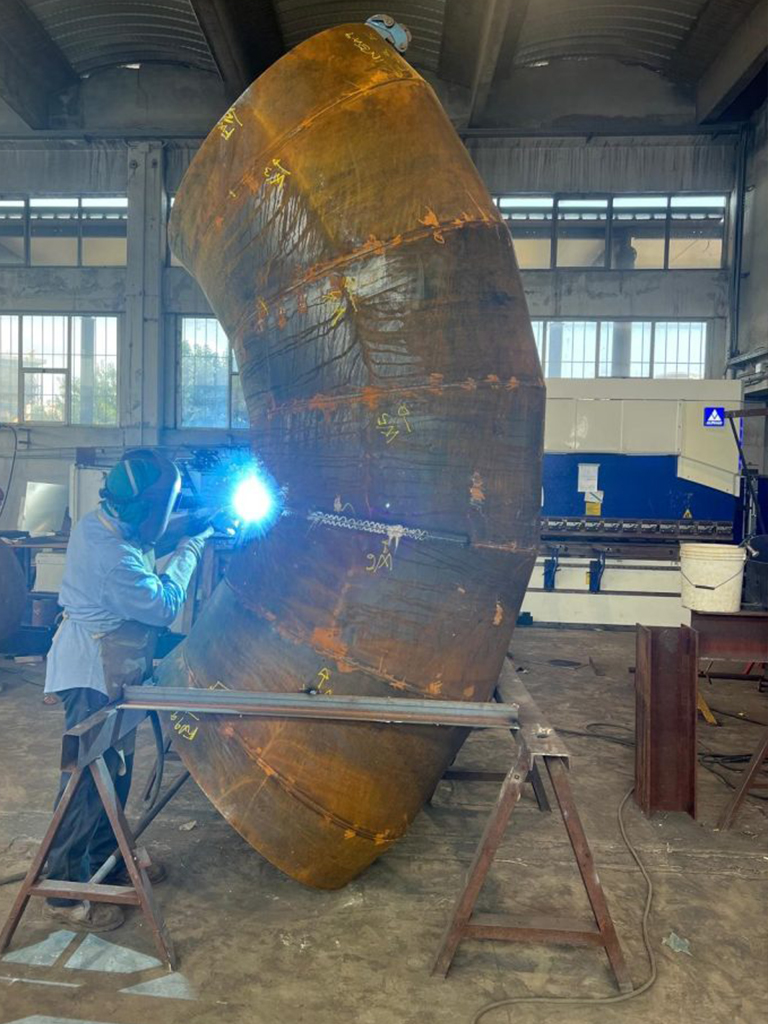

2024: Construction of Flue Gas Ducts, Castellana Grotte (BA) – Centauro Project.
The project involved the design, prefabrication, and installation of flue gas ducts to optimize gas flow and reduce emissions. Activities included the assembly of steel structures, welding, and surface treatment of the ducts to ensure thermal resistance and long-term durability. The work was carried out in compliance with environmental and safety regulations, aiming to enhance the plant’s efficiency and the sustainability of the production process.
2023: Supply, Construction, and Assembly of Steel Structures and Shed for the Inertization Plant – Crotone
The project involved the supply, fabrication, and installation of steel structures and a dedicated shed for an inertization plant in Crotone. The scope of work included the design and assembly of load-bearing steel frameworks, roofing, and cladding to ensure structural stability and durability in an industrial environment. Special attention was given to material selection, corrosion protection treatments, and precision assembly to guarantee compliance with safety and environmental regulations. The construction was executed with a focus on operational efficiency, ensuring seamless integration with existing plant infrastructure while minimizing disruptions to ongoing activities.
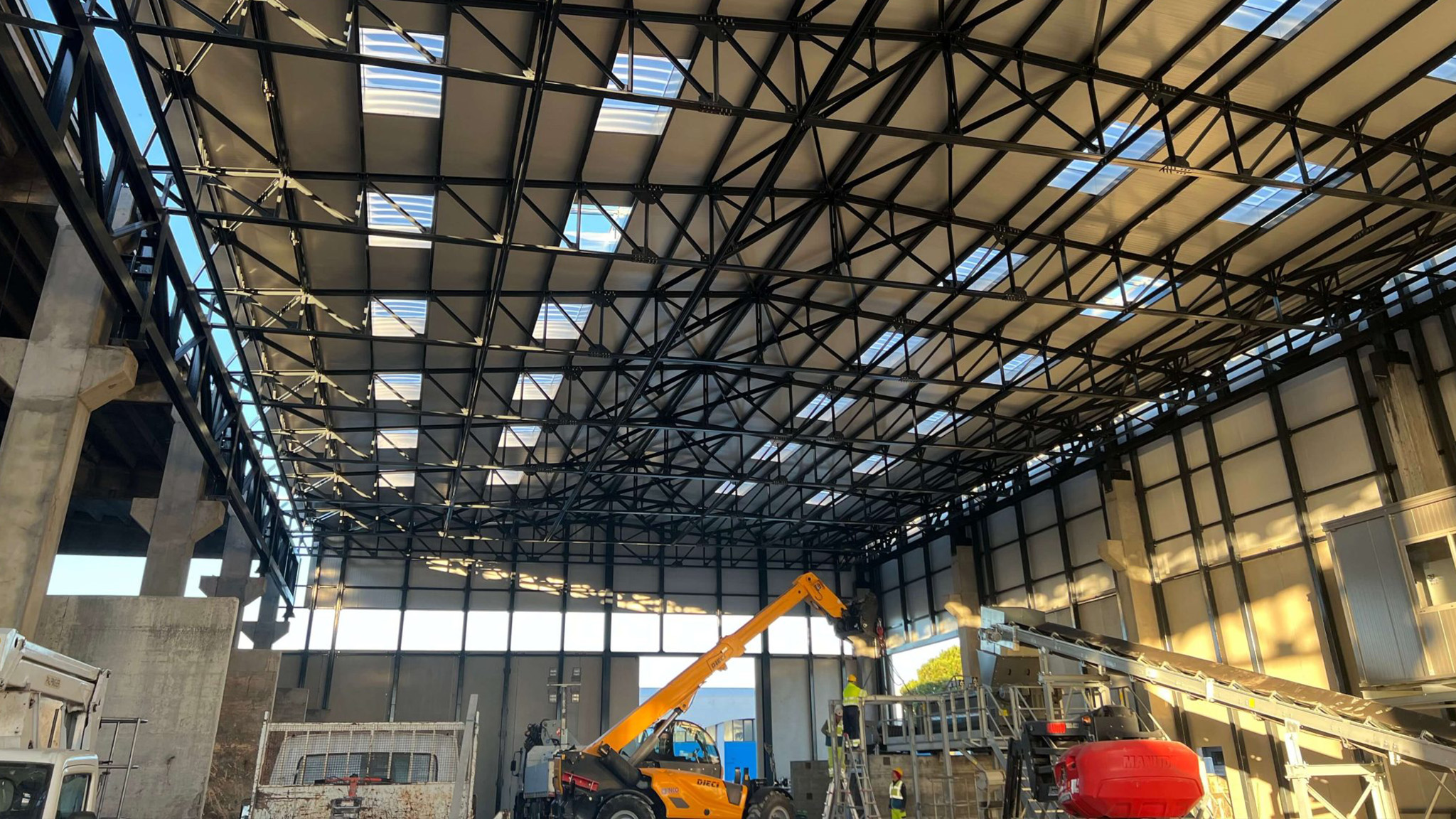
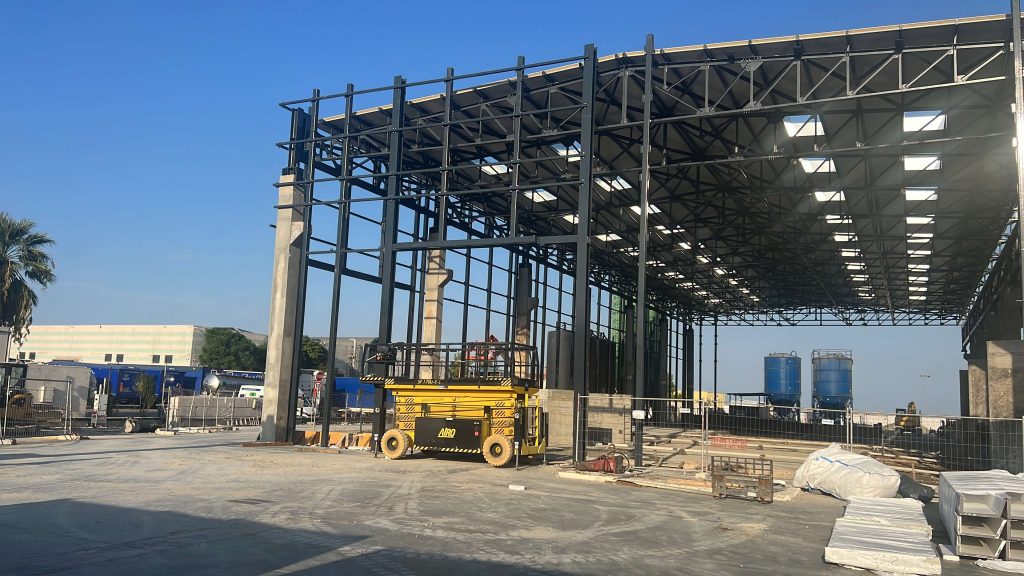
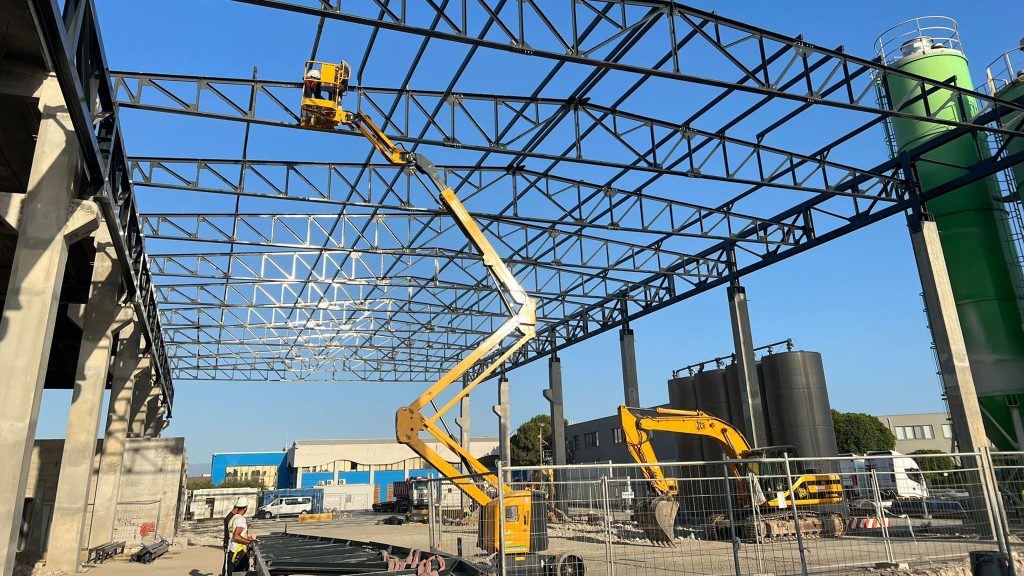
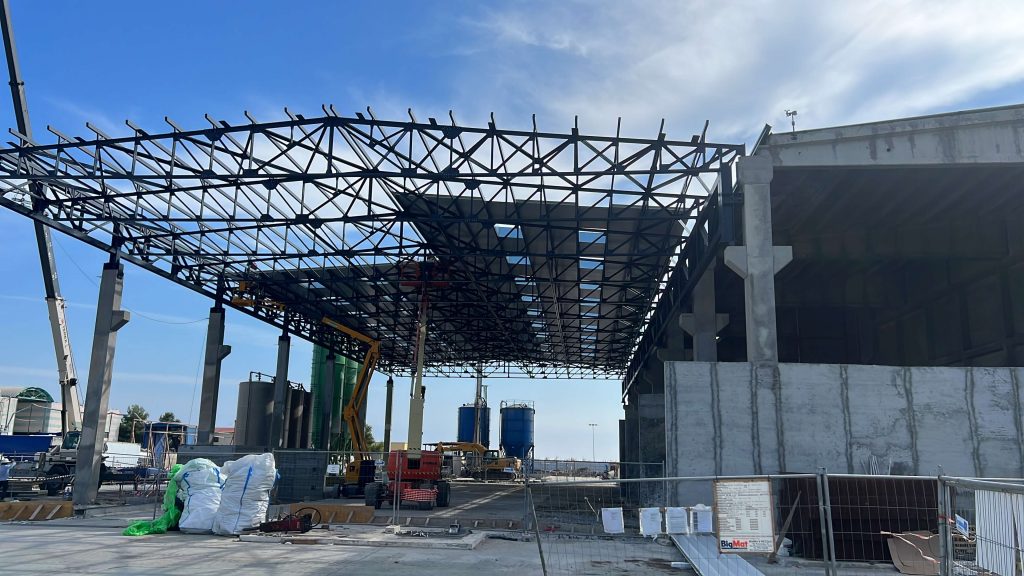
2023: Construction of the Flare – Czech Republic
The project encompassed the engineering, fabrication, and installation of a high-efficiency flare system designed to safely manage and combust excess gases. The scope of work included the assembly of structural components, welding of high-temperature-resistant materials, and the integration of control and safety systems to ensure optimal performance and regulatory compliance. Special attention was given to minimizing environmental impact, improving operational reliability, and adhering to stringent safety standards throughout the construction process.
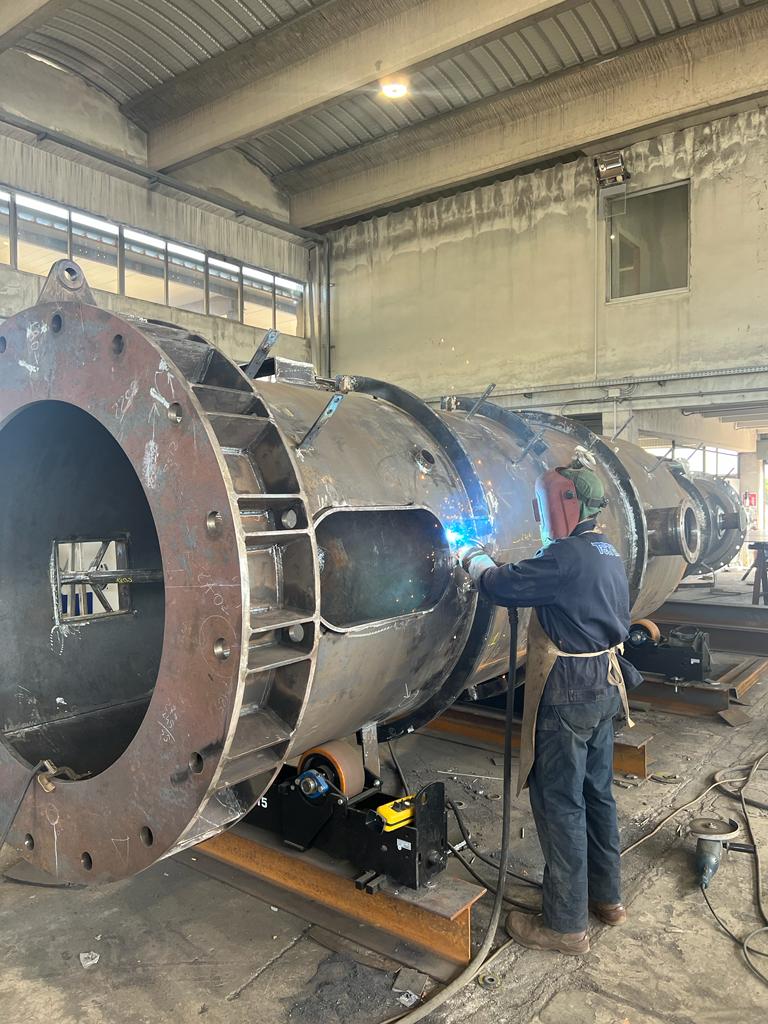
2023: Prefabrication of Piping for the HDT1 Plant (Unit 200), Reforming Plant (Unit 300), and PSA Plant (Unit 450)
The project involved the detailed engineering, fabrication, and quality control of piping systems for critical process units. The scope included precision cutting, welding, and assembly of piping components to meet stringent industry standards and operational requirements. Special attention was given to material selection, non-destructive testing (NDT), and dimensional accuracy to ensure seamless on-site installation. The prefabrication process was carried out under strict safety protocols and compliance with refinery shutdown schedules, minimizing downtime and optimizing plant performance.
Organizational chart
The specialized resources are able to analyze all the phases of the activities, from the planning to the executive one, assuming roles and responsibilities for the various phases of the production cycle.
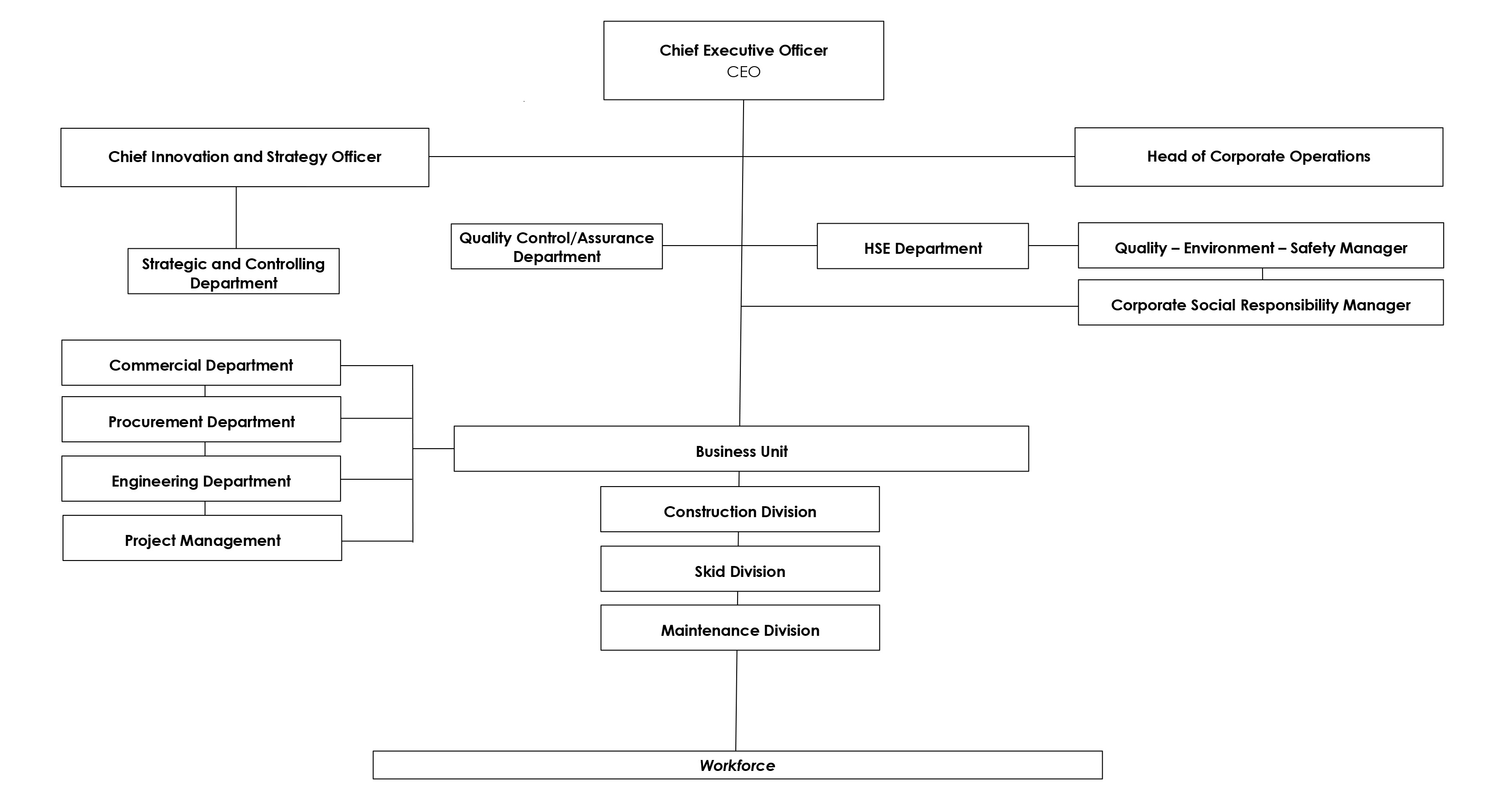
Reference
Fill out the form to request our references